The Problem
The customer needed to be able to unload unevenly loaded containers from the back of a lorry using an existing twin crane system. The containers weighed up to 30,000Kg and could be unequally loaded with the centre of mass being offset towards either end. The customer needed the beam to lock into position on the container without the need for an operator to climb up a ladder or on top of the container to attach or rotate a lift lug.
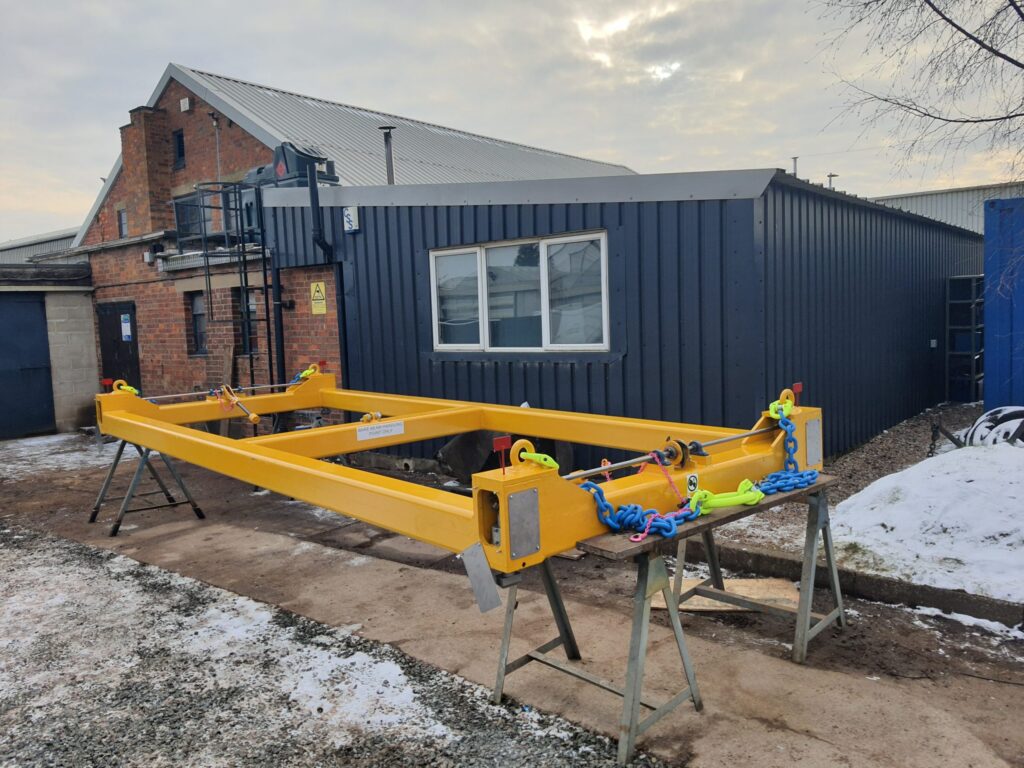
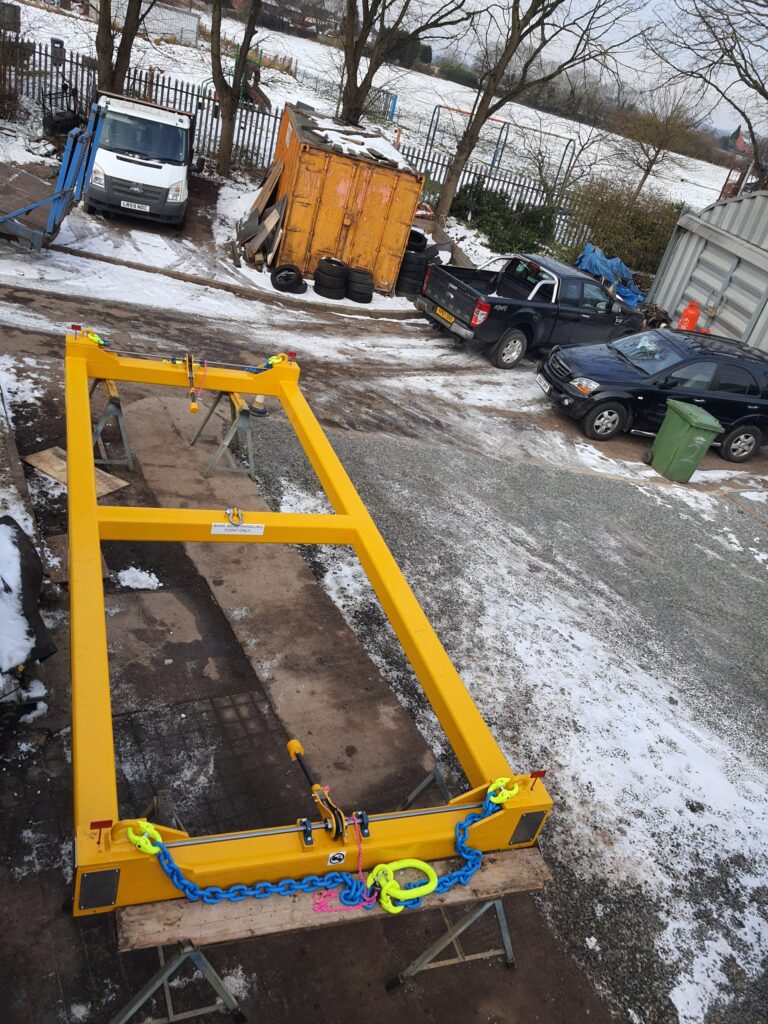
The challenges
The customer wanted to avoid installation of any extra power supplies to the cranes, so any system must mechanically operate solely by the movement of the cranes with the operator being able to recognise whether the beam had engaged securely whilst remaining on the ground.
The mechanism must also be able to disengage once the container has been placed on the ground without intervention from an operator as this would still require the use of a ladder or other equipment to access the top of the container.
Any mechanical components involved in the actuation of the engagement mechanism must be accessible for maintenance and inspection purposes to ensure the ongoing safety and reliability of the lifting mechanism.
The Solution
EDS designed and manufactured a lifting beam which used just the upwards and downwards motion of the cranes to turn specially machined EN24T lifting pins which lock into place once the beam has been landed on top of the container. The same mechanism was also used to disengage the container and would only operate once all the weight of the container had been transferred to either the waiting lorry or on the ground for it to be unloaded.
The beam itself was lifted by two opposing chain assemblies, utilising the existing twin crane system. This twin lift method allowed for the controlled lift of even a considerably unevenly loaded container to be achieved.
The main drive mechanism was housed within the corner fabrications of the beam beneath stainless steel cover plates. This ensured that any dirt was kept out of the mechanism whilst still allowing access for maintenance, inspections and greasing of the components. Indicator flags were also connected directly to the lift pins, allowing the operator to easily see their orientation from a safe distance at ground level to ensure that all the lugs were properly engaged before commencing the lift.
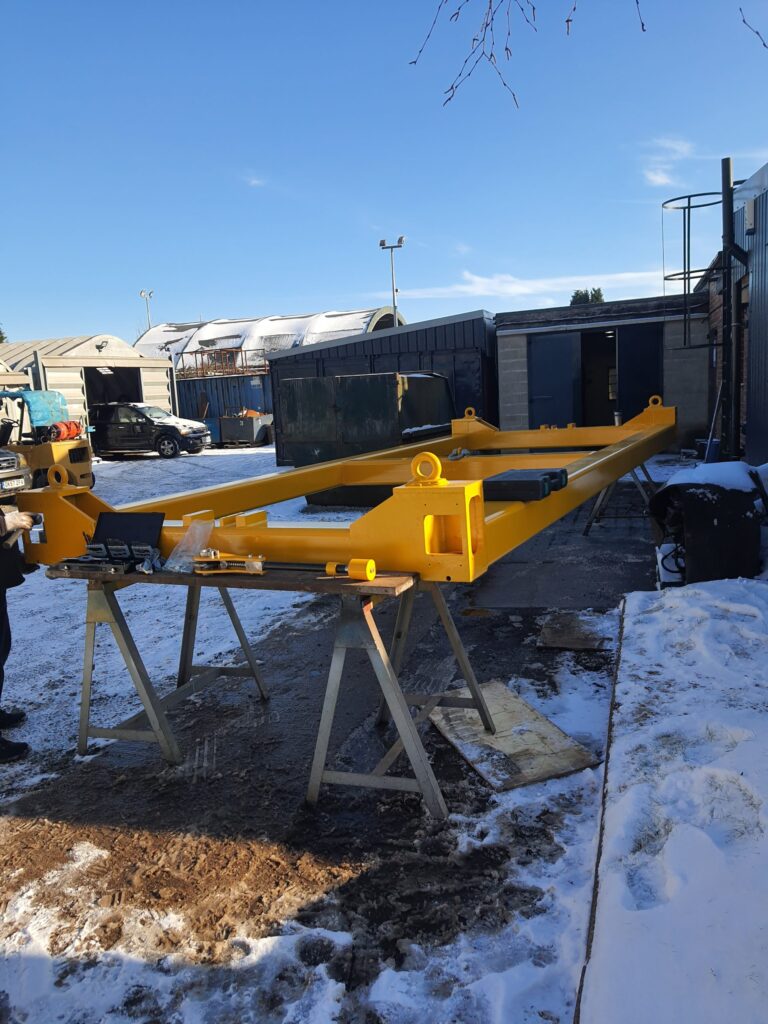